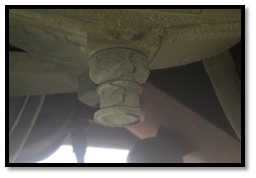
Wheel shelling on wheel tread is a common problem in LHB coaches. This primarily occurs due to partial brake binding. When the brakes are not fully released, some amount of skidding takes place which gives flat spots on wheel tread. If this phenomenon occurs repeatedly, it eventually leads to metal chip off, also known as wheel shelling. As a result, the coach is then marked sick on this account if the length & depth of shelling spot becomes 40 mm or more and 1.5 mm or more respectively. Subsequently, the wheel needs to be changed by detaching the coach from rake. This involves a lot of efforts and a significant cost.
During brake application and release process, air exhaust and intake takes place through a small part present in the brake cylinder integrated unit, known as ‘Breather plug’ (fig.1).During course of time, dust and other foreign particles deposit in the vent hole (fig.2). This obstructs the passage of air due to which brake application and releasing do not take place in a smooth manner, which eventually leads to intermittent skidding, thereby resulting in wheel shelling.
The breather plug was then cleaned properly and installed back (fig.3). This practice was started from 01.02.2018. The condition of wheel before cleaning of breather plug (fig.4, wheel shelling marks can be seen) and after cleaning of breather plug (fig.5, wheel shelling marks have considerably reduced) is shown below. The cleaning of breather plug helps in smooth brake application and releasing, thereby preventing wheel skidding.