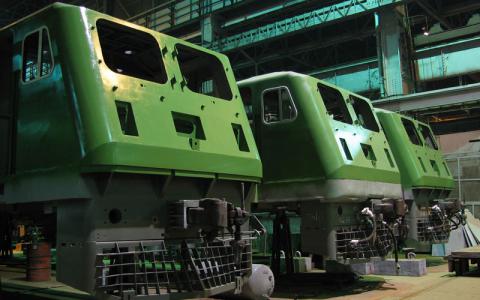
Every component, part and critical asset can tell a story – of its manufacture, of its use, of its possible misuse. DPM is a technology that allows this story to be known – accurately and instantly. The medical screw on the right is used for joining broken bones. It has a squarish mark on the right side in the head – that is DPM at work. Each mark is unique to that piece anywhere across the world, Once marked, always marked, always known.
With DPM, parts and components are marked once with some essential information that allow for its continued track-and-trace through its lifetime. This applies to individual components and also to their assembly. The largest users of DPM technology in India is the automotive sector. From individual fasteners, to piston rings, to rubber components, to even tools used in assembly– all use DPM.
This mark can take several forms dependent on the surface quality. DPM has methods for working with al kinds of surface – rough cast surfaces, machined surfaces, dust-covered surfaces, oil and grease covered surfaces etc. These marks are permanent and cannot fall off or fadeaway.
Interestingly, the encoding system for DPM is the same as the one being currently used for RFID tags for Rolling Stock and major assemblies, such as, bogies. This is an internationally accepted standard by the governing body – GS1. As such, a smooth technological continuum currently exists that allows components along with the final assembly to be treated as one with a common data flow. So a bearing on an axle, fitted on some bogie, being used some coach can be tracked individually and as a whole at the same time.