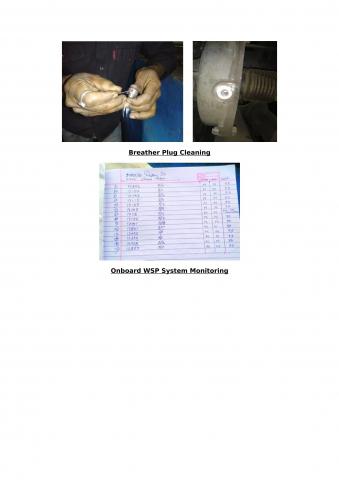
LHB Maintenance Activities carried out at Coaching Depot, Agartala
Besides all maintenance activities that are being carried out routinely at Pitline and Sickline as per maintenance manuals suggested in CAMTECH Manuals, RDSO Manuals and pamphlets etc. there are other maintenance habits that the staffs and supervisors of Coaching Depot, Agartala follows which they consider is of utmost importance for smooth maintenance and running of LHB coaches. Some incidental examples are cited as to why and how these maintenance habits are followed.
“LHB Coaches needs less maintenance”
This above line as we were told during times of training needs better description as we in Coaching Depot, Agartala have practically experienced that the more the precautionary maintenance routine are performed, the lesser the heavier maintenance routine can be avoided. Some incidental example stated here to support the claims i.e. if we maintain healthy WSP system, the lesser is the case of wheel skidding and wheel shelling. And hence the above statement may be understood as, “In LHB Coaches, Better the precautionary maintenance habits, lesser the heavier maintenance required.” The staffs and supervisors of this depot have a better understanding of why things are done as mentioned in CAMTECH and RDSO Manuals and other maintenance routine performed besides the ones mentioned in those manuals.
The Need for Keeping the WSP System healthy
- The healthier the WSP system in an LHB Coach the lesser is the probability of wheel skidding and wheel shelling.
- The staffs in Coaching Depot, Agartala routinely maintain healthy maintenance practice of WSP system during Pitline maintenance of LHB Rakes and also at Sickline. This practice is done routinely as we have observed that a failure or malfunctioning in WSP system can often lead to wheel skidding and in turn wheel shelling.
- Every failure code is attended to and checked in hardware part as well as the processing system. WSP code “99” and “95” is a motto in itself in this depot, even code 95 is attended to check what the fault was and precautionary maintenance habits are performed.
Hardware performance effects WSP performance
- WSP system healthy when both processor and hardware system perform in tandem.
- Besides keeping the WSP system healthy, hardware parts are kept in check routinely. Hardware parts include Brake Caliper Assembly, Brake Cylinder, and pneumatic systems etc.
- Coaching Depot, Agartala practices lubricating of Brake Caliper Assembly fortnightly, cleaning of breather plugs monthly, keeping pneumatic system healthy etc. so that performance of hardware components does not affect WSP performance.
Need for escorting staffs to be alert
- Escorting staffs of Agartala are advised to be alert for incidents and also to keep monitoring the sound of wheel if any and WSP system enroute and onboard so as to detect early failure of Airbrake and WSP system if any.
- They report to base supervisors when failure detected and are advised for further action enroute so that the failure does not affect the coach further.
- Incidental examples: Cases of detention due to C&W faults on Agartala based LHB rakes are less heard of due to alertness of escorting staffs.
- In one case in the year 2018, escorting staff of AGTL-BNC Humsafar, about one hour after departure from BNC, the guard reported smoke fuming from one of the coaches and train was stopped and C&W escorting staffs were called and due to alertness and activeness of the escorting staffs, the brake binding was resolved in 7 minutes and just a total of 14 minutes was detained.
- In another case in AGTL-ANVT Rajdhani Express on 27/03/2019 at around 0300 hrs, escorting staff reported of damaged axle box in one of the coaches, escorting staff previously reported base supervisors of likely failure of WSP system with failure code 72 & 95 & 72 and hence advice the staffs to closely monitor the said coach. The coach was detached at secondary maintenance depot in ANVT for safety concerns but avoided enroute detachment and hence avoided detention due to alertness of escorting staff. Later it was learnt that the problem arise due to phonic cogwheel not being tightened with required torque at the time of SS-1 of the trolley.
Lessons learned from earlier incidents
- Above incidents taught us to keep escorting staffs alert and also to improve maintenance practice further to always check hardware failures once WSP system indicates a failure code even if system rectifies on its own.
- Routine check of tightening torque of SS-1 coaches during inspection at Sickline
Learning what’s being learnt and new experience from experienced OEM staffs
- Experienced staffs from OEM such as Knorr-Bremse regularly invited by respected CDO, Agartala.
- Staffs share experience to OEM staffs for better understanding and troubleshooting of various parts on regular intervals and for refreshing knowledge of why and how things are done.
Active visual examination of parts of trolley
- Vital parts of trolley such as primary suspension springs, secondary suspension springs, dampers, clearances etc. are vigilantly examined at the time of Pitline and Sickline maintenance.
- Understanding how to detect, for instance regular leakage in damper may be due to reduced tension of spring or broken spring; also the same can be detected by checking safety lug clearance etc.
- Bogie body connections are checked vigilantly and also corrosions are checked vigilantly to avoid mishaps.
- Besides bogie parts other vital parts such as couplers are monitored regularly at the time of pit examination as well as at Sickline.