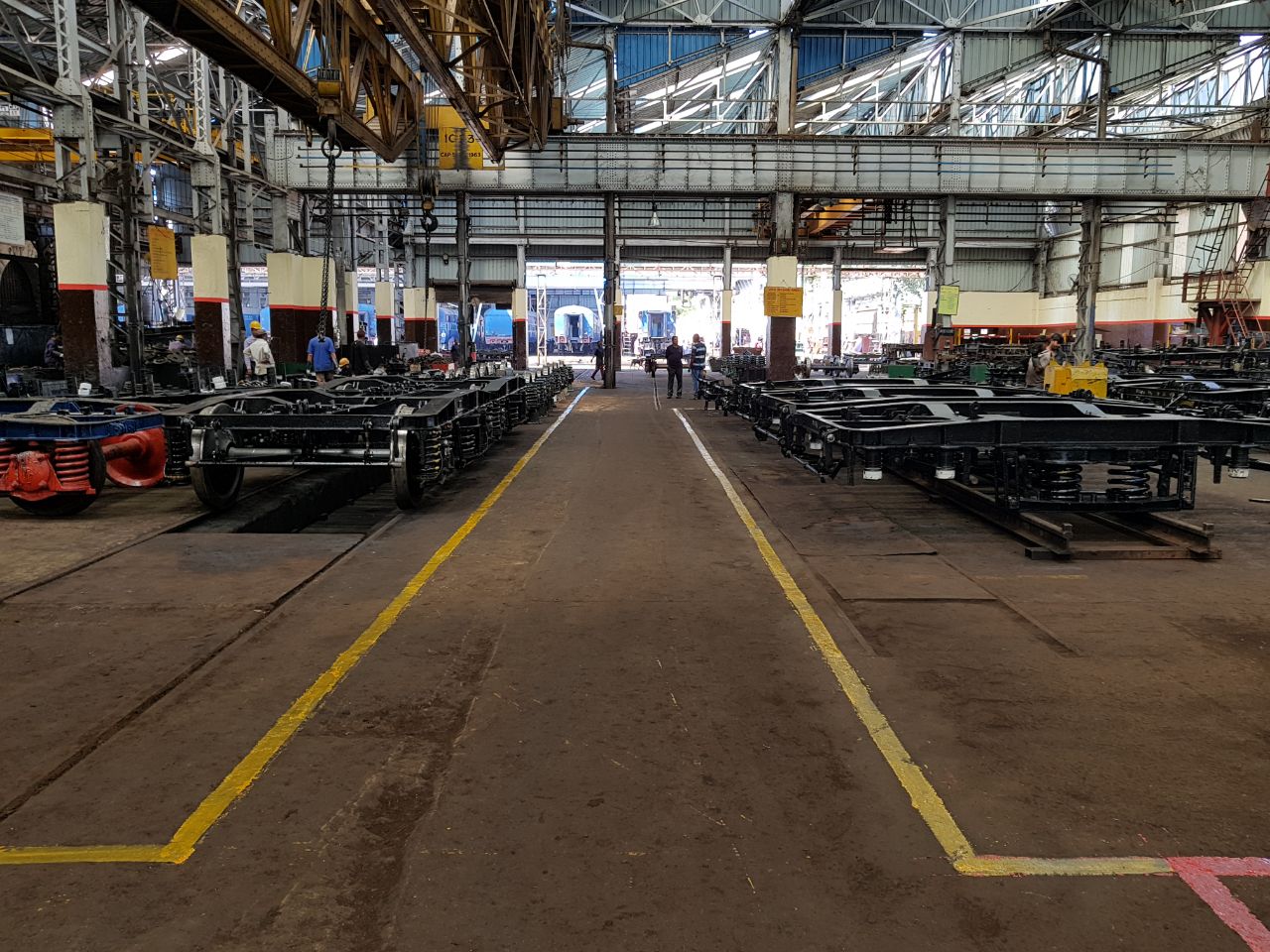
SAFETY:
100% provision of PPE to all workers, which include hard hats, safety gloves, safety shoes, ear dampeners and eye goggles.
Improved lighting in bogie component, bogie assembly, bogie on-wheel and both bogie shop entry. LED lighting is preferred for better light spread and also better efficiency.
Replaced kerosene with suitable water based cleaning agent for component cleaning.
INFRASTRUCTURE:
Provided Industrial flooring in leftover areas of bogie shop (bogie component, bogie assembly, bogie stacking and bogie on-wheel area).
Ample space for Shock Absorber Overhauling room with 3 working areas.Provision of False Ceiling in Shock Absorber Room
BMBC area was converted into stacking area for storage of bogie components such as: alternators and bolster springs.
Bogie stacking is done in current bolster assembly area.
Layout Improvements:
- Bus Bar near rack and in on wheel area is shifted to Main Bus Bar.
- Storage Racks are distributed throughout the shop for efficient storage and reduction in movement of materials.
- Component Painting work station isn shifted, and separate storage bins for different bogie components are used.
- Painting of Pillars
EQUIPMENTS:
Introduction of pressure testing rig for leakage in lower spring seat for better identification of cracks. The said machine was made in-house by Mechanical Millwright Shop
Dot peen marking machines are used for marking of new components to aid tracking during component failure(s)
The Control panel for whiting jacks used in traffic for buffer height adjustment is replaced.
Shotblasting machine: Bogie frame & Components are subjected to shot blasting, to increase identification of cracks, achive better surfacae finish/cleaning, also aids in reduction of failures by increasing quality of inspection.
HOUSEKEEPING:
5s is implemented at bogie shop as a part of house keeping. Provision of various scrap bins with different color codes.
Proper display boards designating each work area with proper description of component and working procedure.